proexcellency
SAP MM Online Training
SAP MM Online training Course With Certification
Proexcellency Provides SAP MM Online Training With Top Consultant Who have 5+Years Realtime Projects experience. SAP MM is an acronym for SAP Material Management. SAP MM is a module within SAP software that is used to manage purchasing, inventory and logistics for a company.
Proexcellency Provides SAP MM Online Training With Top Consultant Who have 5+Years Realtime Projects experience. SAP-MM is an acronym for SAP Material Management. SAP-MM is a module within SAP software that is used to manage purchasing, inventory and logistics for a company. ProExcellency Served 500+ Successful SAP MMOnline Training With 100% satisfactions.
There are many institutes that provide SAP-MM online training courses, but not all of them are equal. The best courses provide high-quality content and are taught by experienced professionals.
Topics |
SAP Introduction & Overview, and Basic Concepts |
Organization Structure & its Configuration |
Execution of Procurement Cycle |
Configuration for Material Master Data |
Configuration for Vendor Master |
Configuration for Purchasing Info Record & Source List |
Configuration for Purchase Requisition & RFQ |
Configuration for Contracts & Scheduling Agreements |
Configuration for Purchase Order Types |
Pricing Procedure |
Release Procedures |
Goods Receipt for Material |
Invoice Verification |
External Services Management |
Inventory Management with SAP MM |
Movement Type Creation |
Configuation for Valuation & Account Determination |
Configuration for Split Valuation |
Consumption Based Planning (CBP) |
Physical Inventory Management |
Automatic PO Process |
Standard Reports |
Cross Functional Customizing |
Overview of SAP MM:
SAP MM (Material Management) is a Module SAP ERP component that enables organizations including material management, inventory management, and warehouse management in the supply chain processes. It is a component of SAP ECC’s logistics functions which includes various components and sub-components. The most outstanding and widely used components are Master Data, Purchasing, and Inventory.
The five major components of the SAP MM are:- Consumption-Based Planning (MM - CBP):
- Purchasing (MM – PUR):
-
External Services Management (MM – SRV):
This component supports bid invitations, order/award placements, acceptance of services and invoice verification. It provides a platform for managing and coordinating external services.
- Inventory Management (MM – IV):
Track and manage physical stocks based on quantity and value and maintain the physical inventory of goods along with planning, entering, and documenting the action of all stocks.
- Logistics Invoice Verification (MM – IV):
The logistics invoice verification is a process that comes at the end of the logistics supply chain. It includes tasks like purchasing, inventory management and invoice verification.
The features of a SAP MM are as follows :
- SAP MM is the module of SAP which deals with material management along with inventory management.
- Material Management as a process allows no shortage of materials or any gaps in the supply chain process of the organization.
- SAP MM advance the procurement and material management activities, making the business run evenly with whole time and cost efficiency.
- SAP MM manage the materials (products and/or services) and resources of an organization with the aim of accelerating productivity and reducing costs.
- SAP MM is quite functional to enclose changes that are recurring in any business environment.
- It serves the Procurement Process, Master Data (Material & Vendor Master), Account Determination & Valuation of Material, Inventory Management, Invoice Verification, Material Requirement Planning and many more.
Organization Structure & its Configuration
In SAP MM training, Proexcellency teaches you the concept of The organisational structure of SAP MM is based on the functional areas of material management. The core functional areas are purchasing, inventory management, and shipping. The purchasing department is responsible for ordering materials, negotiating prices with suppliers, and getting the product at the best price. The Inventory Management Department is responsible for keeping track of the amount of material in the holding stock and making sure that the right amount of material is available when needed. The shipping department is responsible for shipping materials to suppliers and customers.
Execution of Procurement Cycle
The SAP MM procurement cycle is a process that a company goes through to purchase goods and services. The cycle mainly starts with the identification of a need and ends with the receipt of goods or services.
The first step in the purchasing cycle is to determine the need. This can be done in a number of ways, including by viewing sales data, communicating with customers, or browsing vendor directories. Once a need is identified, the company must determine what type of product or service is needed.
Once the need is identified, the company needs to create a purchase requisition. This is a document that outlines the need and provides information about the company, such as contact information and a purchase budget. The purchase requisition is then sent to the appropriate department for approval.
SAP MM (Material Management) Configuration for Material Master Data
This SAP MM online training describes The material master is the main data object in SAP MM. It contains all information about a material, including its attributes, inventory and pricing information, and purchasing and sales data. The material master data record must be set up correctly to ensure transactions are properly processed by the system.
The first step in creating a master data record is to create the basic master data. This includes the material number, description, and manufacturer. The material number is a unique identifier for the material, and the material description is used to identify the material in transactions. A factory is the place where materials are produced or stored.
The second step is to configure the basic features of the material. This includes the different types of material, the characteristics of the plant, and the storage location. The material type is used to define the material class, and the plant-specific attributes are used to store specific information about the material, such as weight or dimensions. Storage location is used to specify the storage location of materials.
The third step is to configure pricing and inventory information. This includes the stock type, stock group, and stock subset. Inventory type is used to specify the different types of inventory, and inventory groups are used to group similar inventory items together. An inventory subgroup is used to group similar inventory items together. Pricing information includes the buying price and the selling price.
The fourth and last step is to configure the purchase and sales data. This includes the purchase order type, purchase order priority, and purchase order group. Purchase order type is used to specify the type of purchase order, and purchase order priority is used to specify the order in which purchase orders are processed. A purchase order group is used to group purchase orders together. The sales order type, sales order priority, and sales order group are used to configure sales data.
This SAP MM online training is for beginners without prior exposure to materials management. SAP MM training will be especially advantageous for those who want to learn how to manage the supply chain management side of the business using SAP so that market requirement can be met in the shortest period of time.
Sap MM software Using Guidance
A step-by-step guide for using SAP MM would include the following steps:
-
Log in to the SAP system using your user ID and password.
-
Then navigate to the MM module by using the menu path or by typing "MM" in the command field and pressing enter.
-
Then familiarise yourself with the various sub-modules within MM, such as purchasing, inventory management, and invoice verification.
-
Then create a purchase request for the materials or services you need.
-
Then Create a purchase order based on the purchase requisition and send it to the vendor.
-
Then monitor the status of the purchase order and approve or reject it as needed.
-
Then Once the materials or services are received, create a goods receipt in the system.
-
After that, perform inventory management tasks such as stock transfers and stock counting.
-
Then verify invoices received from vendors and process payment.
-
last one is running reports to monitor and analyse procurement and inventory performance.
Duration
Duration
30-35 hrs
Shipping & Returns
Shipping & Returns
Dimensions
Dimensions
Care Instructions
Care Instructions
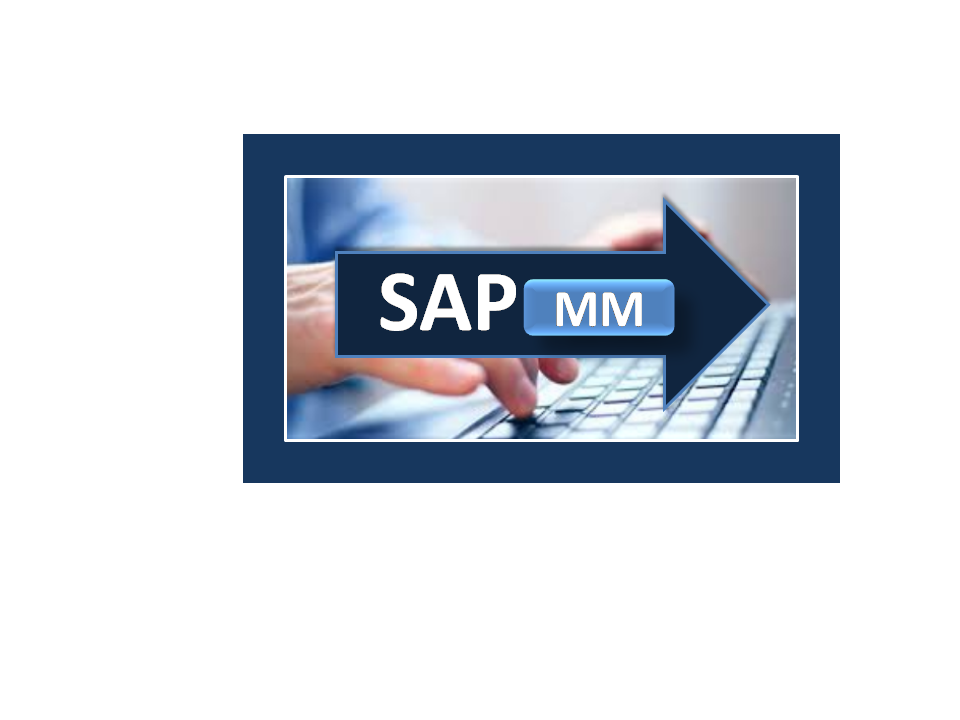